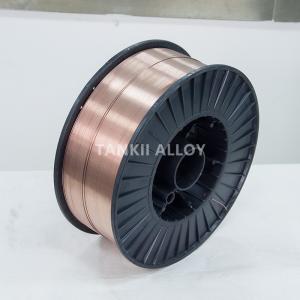
Add to Cart
1.6mm CuSn6 Tin Copper Alloy Spray Wire Copper Coated Color Wire
Thermal spraying means to cause a molten material to collide with and accumulate on the surface of a substrate. Accordingly, in order to create a good thermal spray coating, a high-temperature state to create a sufficient molten state and a high-speed state to spray particles are required. In the film-creation process in thermal spraying, molten particles collide with the substrate and simultaneously become flattened. Some particles become a spray and are scattered. Particles of the raw material that have melted and become a liquid, build up rapidly to form a film.
Method | Coating materials | Substrate materials | Degree of adhesion |
---|---|---|---|
Thermal spraying | Metals, alloys, ceramics, plastics, glass, Cermet | Metals, ceramics, plastics, wood, paper products | Excellent |
Plating | Metals, alloys | Materials that cannot be soaked in the plating solution | Good |
CVD (Chemical Vapor Deposition) | Heat-resistant metals, ceramics, sulfides, selenium compounds, and others | Materials capable of withstanding 500°C-2000°C and chemical corrosion by deposits | Good |
Vacuum deposition | Pure metals, alloys, compounds | Any non-gas-emitting surface | Good Good when substrate heated. Excellent when substrate sputtered. |
Ion plating | Pure metals, alloys, carbides, nitrides, oxides | Same as above | Excellent |
Copper alloy spray wire is a high purity copper wire specifically designed for arc spraying. It produces dense, well bonded coatings with excellent machinability. It is widely used for electrical conductivity and printing roll applications.
The demands for engineering coatings are becoming more and more stringent. Environmental concerns are also being considered as an integral part of the design process. For future economic competitiveness and a lower environmental impact we must therefore turn our attention to processes that use the minimum of resources. Thermal spraying is an attractive coating technique as it offers a wide choice of materials and processes that have a reduced impact on the environment when compared to conventional plating processes.
Thermal spray coating techniques such as HVOF, flame wire spraying, flame powder spraying, arc wire spraying, plasma spraying and cold gas spraying,allow many problems of wear, corrosion and thermal degradation to be resolved by engineering the surface with tailor-made coatings.
Generally speaking, thermal sprayed coatings are a highly cost effective way to add superior performance qualities to a given substrate. The variations on this technical theme are virtually limitless. Coatings can be metallic, ceramic, plastic, or any combination desired to meet a broad range of physical criteria. Thermal sprayed coatings can be the most cost-effective means of protecting substrate surfaces from wear or corrosion. Other primary uses of thermal sprayed coatings include dimensional restoration, maintaining precise clearances, and modifying thermal and electrical properties.